Flange joints are critical components in piping systems, providing secure connections for various applications. This article explores flange joint types and their compatibility with different pipe materials, including mechanical steel pipe, composite pipe for gas, composite pipe for hot water, and composite pipe for plumbing. Additionally, it examines the use of black steel seamless pipe, carbon seamless pipe, and carbon welded steel pipe in flange-based systems. The discussion covers common flange designs, their applications, key installation considerations, and material compatibility.
Common Flange Joint Types for Iron Pipe Fittings
Flange joints are categorized based on design and application requirements. Weld neck flanges feature a tapered hub that provides reinforcement, making them ideal for high-pressure systems using black steel seamless pipe or carbon seamless pipe. The extended neck allows for smooth stress distribution, reducing turbulence at the connection point. These flanges are commonly found in petrochemical plants and power generation facilities where system integrity is paramount.
Slip-on flanges offer easier installation compared to weld neck variants, as they simply slide over the pipe before welding. This design makes them suitable for low to medium pressure applications with carbon welded steel pipe. While not as robust as weld neck flanges, their cost-effectiveness and simple assembly make them popular in water distribution systems and general industrial piping. The inner diameter of slip-on flanges is slightly larger than the pipe's outer diameter to facilitate quick mounting.
Socket weld flanges provide excellent flow characteristics for smaller diameter mechanical steel pipe systems. The pipe inserts into the socket before fillet welding, creating a smooth bore that minimizes pressure drops. These flanges are particularly useful in instrumentation lines and hydraulic systems where flow efficiency is critical. However, they require precise alignment during installation to prevent stress concentrations at the weld points.
Installation and Maintenance of Flange Joints for Iron Pipe Fittings
Proper installation begins with surface preparation to ensure optimal sealing performance. Flange faces must be thoroughly cleaned and inspected for scratches or imperfections before assembly. This is especially important when working with composite pipe for gas systems, where even minor surface defects can lead to leakage. The use of appropriate cleaning solvents and non-abrasive tools helps maintain the flange's sealing surface integrity.
Gasket selection and installation significantly impact joint reliability. For composite pipe for hot water applications, temperature-resistant gasket materials such as graphite or PTFE are recommended. The gasket must be properly centered and compressed evenly during bolt tightening. A crisscross bolt tightening sequence should be followed, gradually increasing torque in multiple passes to achieve uniform load distribution across the flange face. This method prevents warping and ensures consistent gasket compression.
Regular maintenance inspections are crucial for long-term performance. Systems using carbon welded steel pipe should be checked for signs of corrosion or bolt loosening, particularly in environments with thermal cycling. Visual inspections should be supplemented with ultrasonic testing for critical applications. Maintenance schedules should account for the specific service conditions, with more frequent checks required for mechanical steel pipe systems exposed to vibration or mechanical stress.
Material Compatibility of Flange Joints for Iron Pipe Fittings
The selection of flange materials must consider both the pipe composition and service environment. Black steel seamless pipe and carbon seamless pipe typically pair with carbon steel flanges in high-pressure applications. The matching of material properties ensures similar thermal expansion characteristics and weldability. For corrosive services, stainless steel flanges may be specified even when connecting to carbon steel pipes, with appropriate isolation methods to prevent galvanic corrosion.
Composite pipe for gas and composite pipe for hot water present unique challenges due to their different thermal expansion rates compared to metal flanges. In these cases, flanges with insulating gaskets or special adapters are used to accommodate differential movement. The flange design must also account for the lower mechanical strength of composite materials, often requiring support collars or reinforced flange faces to distribute clamping forces properly.
When working with composite pipe for plumbing systems, consideration must be given to chemical compatibility. The flange gasket material must resist degradation from both the conveyed fluid and any cleaning agents used in the system. Plastic flanges or metal flanges with plastic liners are common choices, offering corrosion resistance while maintaining adequate mechanical strength for residential and commercial plumbing applications.
Flange joints are essential for reliable piping systems across industries. The selection of flange joint types depends on factors such as pressure, temperature, and pipe material, including mechanical steel pipe, composite pipe for gas, and carbon welded steel pipe. Understanding the strengths of black steel seamless pipe and carbon seamless pipe helps optimize flange performance. By matching flanges with appropriate materials, such as composite pipe for hot water or composite pipe for plumbing, engineers ensure long-term system integrity. Proper installation and maintenance further enhance the efficiency of flange-connected pipelines.
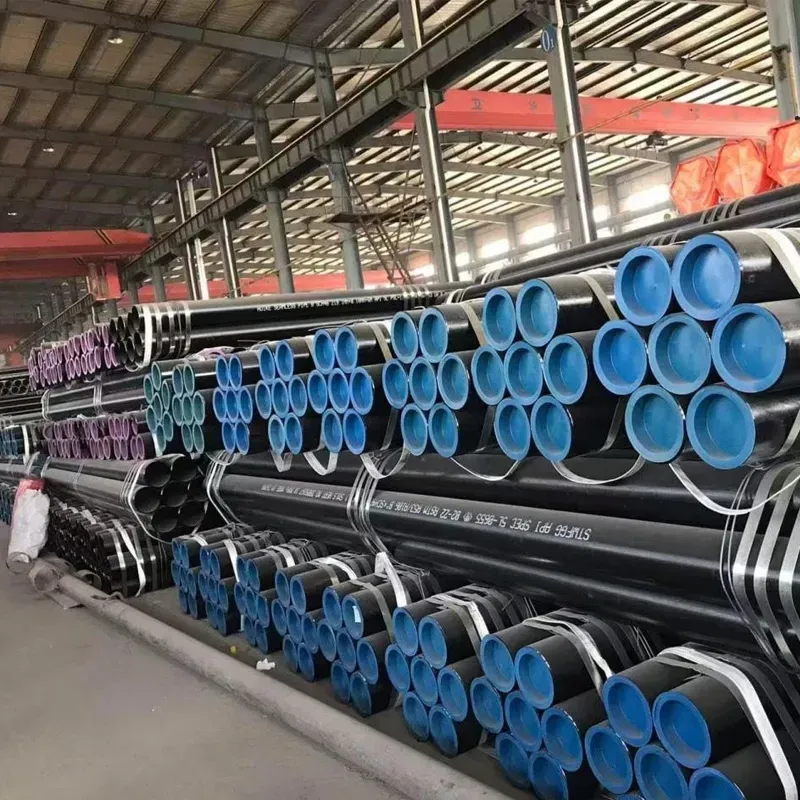