Flanges are essential components in various industrial systems, playing a crucial role in connecting pipes, valves, pumps, and other equipment. Different types of flanges serve specific purposes, and understanding their characteristics and applications is key to ensuring the integrity and efficiency of industrial setups. In this exploration, we'll delve into the world of metric flanges, mild steel flanges, motor flanges, mounting flanges, and ms flanges, uncovering their unique features and the vital functions they perform.
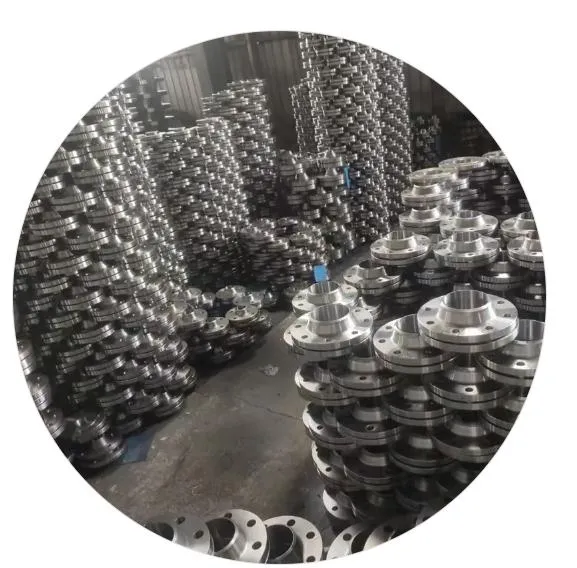
The Precision and Standardization of Metric Flanges
In the realm of industrial piping systems, metric - based measurements bring a level of precision and standardization. Metric flanges are designed according to specific international standards that define their dimensions, pressure ratings, and connection types. These flanges are widely used in regions that adhere to the metric system, facilitating seamless integration of piping components across different manufacturers. For instance, in European industrial plants, metric flanges ensure that pipes of varying lengths and diameters can be securely joined together. The standardized bolt hole patterns and face profiles of metric flanges mean that replacement parts can be easily sourced, reducing downtime during maintenance and repair operations. Their ability to handle different pressure ranges makes them suitable for a variety of applications, from low - pressure water distribution systems to high - pressure industrial fluid transfer setups.
The Durability and Versatility of Mild Steel Flanges
Mild steel flanges, also known as ms flanges, are highly valued for their durability and cost - effectiveness. Composed of mild steel, which contains a relatively low percentage of carbon, these flanges offer good strength and formability. In construction projects, mild steel flanges are commonly used to connect structural steel members. They can withstand significant loads and stresses, ensuring the stability of buildings and bridges. In the oil and gas industry, ms flanges are employed in pipelines to transport hydrocarbons. Their resistance to corrosion, especially when properly coated or treated, makes them suitable for both onshore and offshore applications. Whether it's in a refinery where they help transfer refined products or in a natural gas processing plant, mild steel flanges provide a reliable connection solution that can endure harsh operating conditions.
Motor Flanges: Integral to Machinery Operation
When it comes to motors and rotating machinery, motor flanges play an indispensable role. These flanges are specifically designed to connect the motor to other components, such as pumps, fans, or conveyors. The motor flange serves as a mounting surface that ensures proper alignment between the motor shaft and the driven equipment. A well - designed motor flange reduces vibration and minimizes the risk of premature wear and tear on the motor and connected machinery. For example, in an industrial manufacturing facility, a motor flange on an electric motor driving a conveyor belt ensures smooth and consistent operation. It allows for easy installation and removal of the motor during maintenance, without disrupting the entire production line. The material and construction of motor flanges are carefully engineered to handle the torque and rotational forces generated by the motor, providing a secure and reliable connection.
Mounting Flanges: The Foundation for Secure Attachments
Mounting flanges act as the foundation for securely attaching various equipment and components. They come in different shapes and sizes, tailored to the specific requirements of the application. In the automotive industry, mounting flanges are used to attach engines, transmissions, and other critical components to the vehicle chassis. These flanges are designed to absorb shock and vibration, enhancing the overall ride comfort and durability of the vehicle. In the aerospace sector, mounting flanges are crucial for attaching aircraft engines, wings, and other structural elements. Precision - engineered mounting flanges ensure that these components are correctly positioned and can withstand the extreme forces experienced during flight. Whether it's in a manufacturing plant, a vehicle, or an aircraft, mounting flanges provide a stable and secure attachment point, enabling the safe and efficient operation of equipment.
FAQs about Specialized Flanges
How to Select the Right Flange for a Specific Application?
Selecting the appropriate flange depends on several factors. First, consider the operating pressure and temperature of the system. For high - pressure applications, flanges with higher pressure ratings, such as those made of stronger materials or with specific designs, are required. The type of fluid or gas being transported also matters, as some substances may be corrosive and demand flanges with appropriate corrosion - resistant properties. Additionally, the connection type, whether it's a weld - neck, slip - on, or blind flange, should be chosen based on ease of installation, maintenance, and the specific requirements of the piping or equipment setup.
What Are the Maintenance Requirements for Mild Steel Flanges?
Mild steel flanges require regular inspection to check for signs of corrosion, cracks, or deformation. Periodic cleaning and removal of dirt, debris, and any corrosive substances that may accumulate on the surface are essential. If corrosion is detected, the affected area may need to be cleaned, treated, and potentially recoated with a protective layer, such as paint or a corrosion - resistant coating. Bolts and gaskets associated with mild steel flanges should also be inspected and tightened as needed to ensure a secure seal and prevent leakage.
Can Motor Flanges Be Interchanged Between Different Motor Models?
In general, motor flanges are designed specifically for certain motor models and their associated driven equipment. Interchanging motor flanges between different motor models is not recommended without careful consideration. The flange's dimensions, bolt hole patterns, and the alignment of the motor shaft with the driven equipment are all critical factors. Even if the physical size of the flanges appears similar, differences in these key aspects can lead to improper alignment, excessive vibration, and potential damage to the motor and connected machinery. It's advisable to use flanges that are specifically designed and recommended for the motor and application at hand.