Steel pipes are essential components in various industries, serving as conduits for fluids, gases, and structural supports. Their versatility stems from different manufacturing techniques, materials, and customization options. This article explores the fundamentals of tubular steel, its classifications, manufacturing processes, and applications, with a focus on customized steel pipe solutions. Key variations such as thick wall stainless steel tubes, thin steel pipes, and multilayer composite pipes will be examined to highlight their distinct uses.
Types and Classifications of Stahlrohre
The classification of steel pipes primarily depends on their dimensional specifications and intended applications. Thin steel tube products, typically with wall thicknesses below 3mm, are favored in applications where weight reduction is critical without compromising structural integrity. These are commonly seen in automotive fuel lines, refrigeration systems, and furniture frameworks. On the opposite spectruthick-walledall stainless steel tube varieties with wall thicknesses exceeding 10mm are engineered to withstand extreme pressures in petrochemical plants and power generation facilities.
Material composition further divides steel pipes into distinct categories. Carbon steel pipes dominate general industrial applications due to their cost-effectiveness and reliable strength. Stainless steel variants offer superior corrosion resistance, making them indispensable in food processing and pharmaceutical industries. The emergence of alloy steel pipes has bridged the gap between strength and corrosion resistance, particularly in offshore drilling operations and chemical processing plants where both properties are equally crucial.
Manufacturing methods create another layer of classification. Seamless pipes, produced through extrusion or rotary piercing, provide uniform strength throughout their structure. Welded pipes, formed by rolling and joining steel plates, offer economic advantages for large-scale projects. Recent advancements have introduced laser-welded options that combine the precision of seamless pipes with the cost benefits of traditional welded varieties, particularly useful in precision instrumentation and aerospace applications.
Key Industries Using Stahlrohre
The construction sector remains one of the largest consumers of steel pipe products. Welded galvanized pipe serves as the backbone of modern infrastructure, providing durable solutions for water supply networks, scaffolding systems, and building frameworks. The galvanization process extends the service life of these pipes significantly, especially in coastal areas where saltwater corrosion poses constant challenges. High-rise buildings particularly benefit from the structural stability offered by steel pipe columns and beams.
Energy industries rely heavily on specialized steel pipe solutions. The oil and gas sector utilizes thick-walled stainless steel tubes for both upstream exploration and downstream processing. These pipes must endure extreme pressures in deep-sea drilling operations while resisting corrosion from sour gas components. Similarly, power generation plants employ high-grade steel pipes in boiler systems and steam lines, where temperatures can exceed 600°C. Nuclear facilities demand even more stringent specifications, often requiring customized alloy compositions to ensure radiation containment.
Manufacturing and transportation sectors have developed unique applications for steel pipes. Automotive manufacturers prefer thin steel pipe for exhaust systems and chassis components, where weight reduction directly impacts fuel efficiency. The aerospace industry uses precision-engineered tubular steel in hydraulic systems and airframe structures. Even consumer goods industries incorporate steel pipes in everything from bicycle frames to household appliances, demonstrating the material's unparalleled versatility across scales of production.
Manufacturing and Customization of Stahlrohre
Modern steel pipe production has evolved into a highly sophisticated process with numerous quality control measures. The initial stage involves careful selection of raw materials, where steel billets or coils are inspected for chemical composition and structural integrity. For seamless pipes, the hot rolling process begins with heating the billet to approximately 1200°C before extrusion through a mandrel mill. Welded pipe production employs continuous cold forming of steel coils, with the edges joined through high-frequency induction welding or submerged arc welding for thicker walls.
Customization plays an increasingly vital role in meeting specific industrial requirements. Customized steel pipe solutions now encompass not just dimensional adjustments but also material enhancements. For cryogenic applications, pipes undergo special heat treatment to prevent brittleness at low temperatures. The medical field requires ultra-precise thin steel tubes with mirror-finish interiors to prevent bacterial growth. In the semiconductor industry, ultra-clean pipes with electropolished surfaces ensure contamination-free gas delivery systems.
Post-production treatments significantly expand the functional capabilities of steel pipes. Galvanization remains the most common protective coating, with hot-dip galvanizing providing superior protection for weld galvanized pipe used in outdoor applications. More advanced options include epoxy coatings for chemical resistance and ceramic linings for abrasion resistance in mining operations. Recent developments in nanotechnology coatings promise even greater protection against corrosion and fouling, particularly for multilayer composite pipe systems in desalination plants and offshore platforms.
Steel pipes remain indispensable across multiple sectors due to their adaptability and durability. From thin steel tube applications in electronics to thick-walled stainless steel tube usage in heavy industry, the material's versatility is evident. Innovations like pipe composite technology continue to expand their applications, ensuring efficiency in fluid transport, construction, and mechanical systems.
The ability to produce customized steel pipe solutions further solidifies their role in modern engineering. As industries evolve, advancements in multi-layer composite pipe designs and corrosion-resistant treatments will drive future developments, reinforcing steel pipes as a cornerstone of industrial infrastructure. Emerging trends such as smart pipes with embedded sensors for real-time monitoring and self-healing coatings point toward an even more innovative future for this fundamental industrial material.
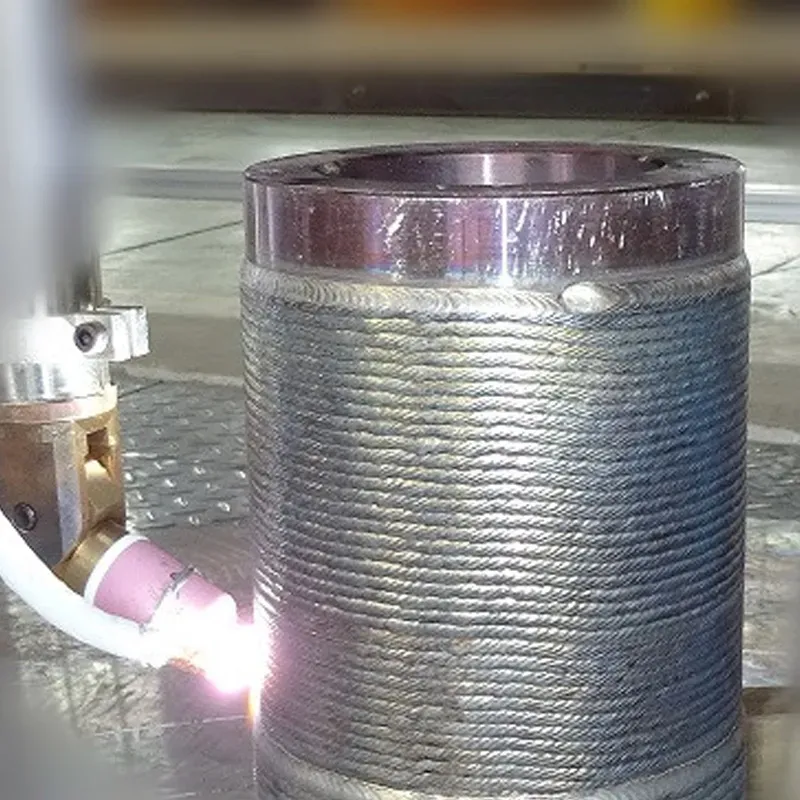