Corrosion is a major challenge in industrial and infrastructure applications, leading to material degradation, increased maintenance costs, and potential safety hazards. Anti-corrosion steel pipe provides an effective solution by combining durable materials with advanced protective coatings, ensuring long-term performance in harsh environments. These pipes are essential in industries such as oil and gas, chemical processing, water distribution, and heating systems, where resistance to rust, chemicals, and extreme temperatures is critical.
Understanding Anti-Corrosion Steel Pipe and Its Importance
The fundamental purpose of anti-corrosion steel pipe lies in its engineered resistance to oxidation and chemical breakdown. Unlike standard steel pipes that may deteriorate rapidly when exposed to moisture or aggressive substances, these specialized pipes incorporate protective measures at both material and surface treatment levels. The base material often consists of high-grade steel alloys, with carbon steel A106 and A106B carbon steel, being particularly favored for their balanced properties of strength and workability. These materials serve as excellent substrates for additional protective layers.
Surface treatments play an equally crucial role in enhancing corrosion resistance. Common methods include hot-dip galvanization, where pipes are coated with a layer of zinc to create a sacrificial barrier. More advanced options involve epoxy or polyethylene coatings applied through sophisticated processes like electrostatic spraying or extrusion wrapping. Such treatments not only prevent direct contact between the steel and corrosive elements but also provide additional benefits like improved abrasion resistance. In marine or underground applications, cathodic protection systems may be integrated with anti-corrosion steel pipes to further extend service life through electrochemical means.
Types of Anti-Corrosion Steel Pipes and Their Uses
The diversity of anti-corrosion steel pipe products addresses varying industrial requirements through specialized designs. Pre-insulated black steel pipe represents a significant category, featuring both corrosion protection and thermal insulation in a single unit. These pipes typically consist of a steel core wrapped in moisture-resistant insulation material, all encased in a protective outer jacket. This design proves particularly valuable in district heating networks where maintaining fluid temperature is as important as pipe durability. Similarly, pre-insulated carbon steel pipe offers enhanced thermal performance for applications ranging from industrial process lines to geothermal systems.
For high-pressure applications, carbon seamless steel pipes provide superior reliability due to their homogeneous structure without welded seams. The absence of weld lines eliminates potential weak points where corrosion might initiate, making these pipes ideal for critical services in power plants and refineries. When mechanical strength needs to be combined with chemical resistance, composite tube solutions come into play. These innovative products layer different materials, typically with a steel structural core and polymer protective lining, to achieve optimal performance characteristics. The square-profile variants, known as composite square tubing, find particular utility in structural applications where both corrosion resistance and load-bearing capacity are required.
Fluid transfer systems often employ flexible alternatives like composite hose pipe, which combines metal reinforcement with synthetic liners to handle aggressive chemicals while maintaining flexibility. In building services, composite plumbing pipe systems are increasingly replacing traditional materials due to their corrosion-free performance and ease of installation. These composite solutions demonstrate how material science innovations continue to expand the capabilities of anti-corrosion steel pipes across multiple sectors.
Manufacturing and Quality Assurance of Anti-Corrosion Steel Pipes
The production of anti-corrosion steel pipe begins with stringent material selection, where steel grades like carbon steel A106 are chosen for their optimal chemical composition and mechanical properties. Modern manufacturing employs either seamless or welded methods, with seamless pipes created through rotary piercing and elongation processes, while welded pipes undergo forming and electric resistance welding. Surface preparation is critical, involving abrasive blasting and chemical treatments to ensure proper coating adhesion. Various protective systems are then applied, including fusion-bonded epoxy coatings through electrostatic spraying or extruded polyethylene layers, while pre-insulated carbon steel pipe receives additional polyurethane foam injection between the pipe and outer casing.
Quality assurance is maintained through rigorous testing at every production stage. Non-destructive methods like ultrasonic inspection verify wall thickness and detect flaws, while hydrostatic testing confirms pressure containment capability. Finished pipes undergo coating integrity checks using holiday detection systems, and insulation properties are verified through thermal conductivity testing. Manufacturers adhere to international standards such as ASTM, API, and ISO to ensure anti-corrosion steel pipe products meet the demanding requirements of global industries, guaranteeing both performance and longevity in challenging applications.
Anti-corrosion steel pipe plays a vital role in modern infrastructure by combining durability with advanced corrosion protection. From standard carbon steel A106 pipes to innovative composite tube solutions, these products meet diverse industrial needs while reducing maintenance costs. As material science advances, future developments will further enhance their performance and expand applications across critical industries. With its proven reliability and evolving technology, anti-corrosion steel pipe remains an essential solution for long-term piping requirements.
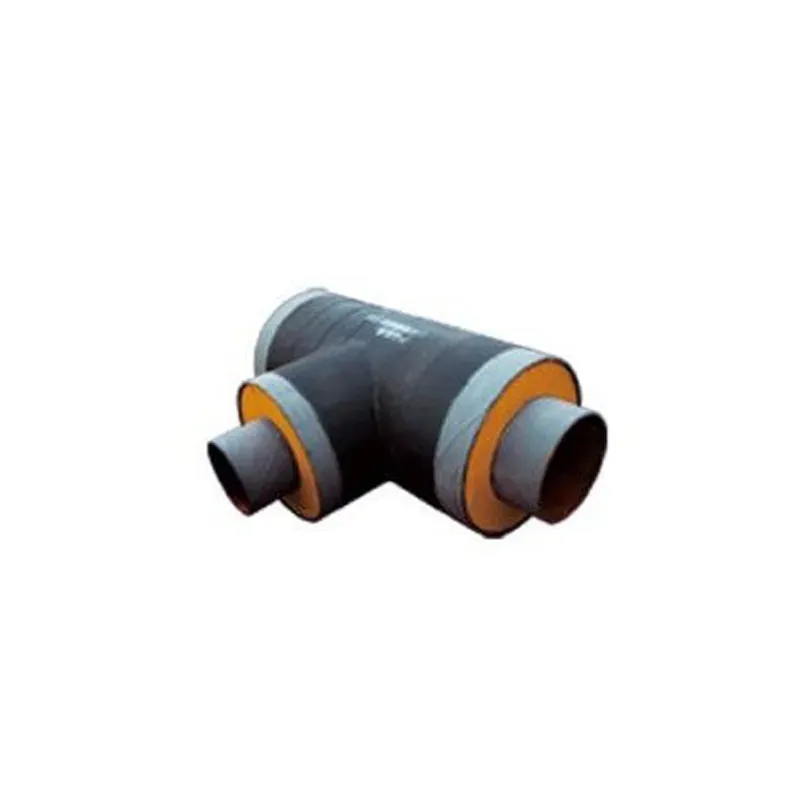