Alloy steel pipe is a critical component in various industrial applications due to its enhanced mechanical properties and resistance to extreme conditions. This article explores the composition, manufacturing processes, and primary uses of alloy steel pipe, comparing it with alternatives such as seamless carbon steel tube, aluminium composite pipe, and carbon steel reducer. The discussion also covers key industry standards, including carbon steel A106, and concludes with an overview of its long-term benefits.
Composition and Manufacturing of Alloy Steel Pipe
Alloy steel pipe is engineered by blending iron with elements such as chromium, nickel, molybdenum, or vanadium. These additions enhance hardness, tensile strength, and resistance to wear and corrosion. Unlike seamless carbon steel, which relies primarily on carbon content for strength, alloy steel incorporates multiple metals to achieve tailored performance characteristics. The precise composition varies depending on the intended application, ensuring optimal performance in different environments.
The production of alloy steel pipe involves either seamless or welded methods. Seamless pipes are formed through extrusion or rotary piercing, resulting in a uniform structure ideal for high-pressure applications. Welded pipes, constructed from rolled steel plates, are more economical but may have weaker points along the seams. When compared to aluminum composite pipe, which combines aluminum and plastic layers for flexibility, alloy steel pipe provides greater structural integrity and thermal stability, making it suitable for heavy-duty industrial use.
Quality control is a crucial aspect of manufacturing alloy steel pipe. Standards such as ASTM A335 and ASME SA213 ensure consistency in mechanical properties and dimensional accuracy. Heat treatment processes, including quenching and tempering, further refine the material’s strength and ductility. These rigorous procedures distinguish alloy steel pipe from alternatives like carbon steel A106, which follows less stringent requirements for moderate-temperature applications.
Key Properties and Performance of Alloy Steel Pipe
The defining characteristics of alloy steel pipe include high tensile strength, resistance to oxidation, and the ability to perform under extreme temperatures. These properties make it indispensable in industries such as petrochemicals, power plants, and aerospace. Unlike seamless carbon steel tube, which may degrade under prolonged exposure to high heat or corrosive substances, alloy steel pipe maintains structural integrity even in harsh conditions.
Another advantage is its adaptability to different environments. For example, chromium-molybdenum alloys enhance resistance to sulfur and hydrogen-induced cracking, making them ideal for oil refineries. In contrast, aluminum plastic composite pipe is limited to low-pressure plumbing and HVAC systems due to its lower melting point and reduced load-bearing capacity. The versatility of alloy steel pipe ensures its dominance in applications where reliability is non-negotiable.
Furthermore, alloy steel pipe exhibits excellent weldability and machinability when proper techniques are applied. Preheating and post-weld heat treatment minimize the risk of cracking, ensuring long-term durability. While carbon steel reducer fittings are commonly used in standard piping systems, alloy steel pipe is preferred in critical installations where failure is not an option.
Industrial Applications of Alloy Steel Pipe
The oil and gas industry extensively relies on alloy steel pipe for drilling, transportation, and refining processes. Its resistance to sour gas (hydrogen sulfide) and high-pressure conditions makes it superior to carbon steel A106, which is typically used in less demanding scenarios. Offshore platforms and pipelines particularly benefit from the corrosion-resistant properties of alloy steel, ensuring long-term operational safety.
In power generation, alloy steel pipe is used in boilers, superheaters, and steam lines where extreme temperatures and pressures are common. Unlike aluminium composite pipe, which cannot withstand such conditions, alloy steel ensures efficient energy transfer without structural compromise. Nuclear power plants also utilize specialized grades of alloy steel pipe due to their radiation resistance and mechanical stability.
The construction and automotive industries also employ alloy steel pipe for structural frameworks and high-stress components. While carbon steel reducer fittings are sufficient for standard piping connections, alloy steel pipe is chosen for critical load-bearing structures. Its combination of strength and lightweight efficiency (compared to solid steel) makes it a preferred material in modern engineering projects.
Alloy steel pipe remains a superior choice for industries that demand durability, high performance, and resistance to extreme conditions. Its customizable composition allows it to outperform alternatives like seamless carbon steel tube and aluminum plastic composite pipe in critical applications. The rigorous manufacturing standards and heat treatment processes further enhance its reliability, making it indispensable in sectors such as oil and gas, power generation, and heavy construction.
While materials like carbon steel A106 and aluminium composite pipe serve specific purposes in less demanding environments, alloy steel pipe provides unmatched longevity and structural integrity. As industrial requirements continue to evolve, the adaptability and strength of alloy steel pipe ensure its continued relevance in advanced engineering and infrastructure development.
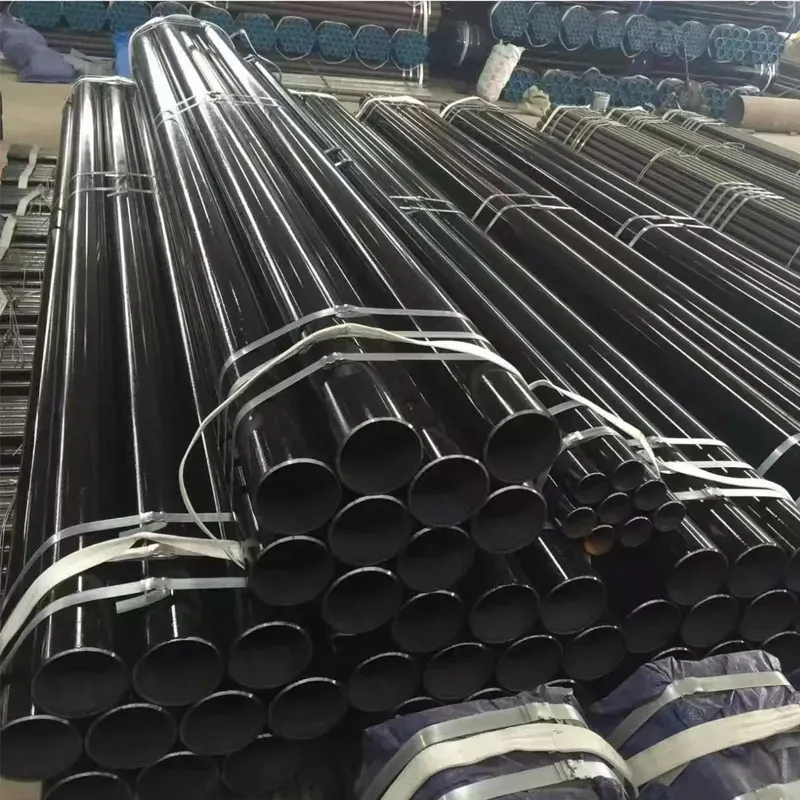