Pipeline fittings serve as critical connection points in fluid transportation systems across multiple industries. These components enable directional changes, branch connections, and diameter transitions while maintaining structural integrity under various pressure and temperature conditions. The selection of appropriate fittings, such as black steel elbows, carbon steel tees, and reducer pipe, requires careful consideration of material properties, operating conditions, and industry specifications. This examination covers the classification, industrial uses, and technical selection parameters of modern pipeline fittings.
Pipeline Fitting Types
Elbow fittings represent one of the most fundamental categories in piping systems, primarily designed to alter flow direction. The black steel elbow serves as a standard solution for general-purpose applications, offering reliable performance in low to moderate pressure systems. For more demanding environments, the black steel pipe elbow enhances durability with its thicker wall construction. The carbon steel 90-degree elbow is specifically engineered for applications requiring precise right-angle turns while maintaining optimal flow characteristics and structural integrity.
Tee fittings constitute another essential group, facilitating flow division or combination within piping networks. Standard carbon steel tee fittings create equal distribution branches, commonly used in water supply and industrial process lines. When connecting pipes of different diameters becomes necessary, the carbon steel reducing tee offers an efficient solution with its tapered design. For high-pressure systems and critical applications, the forged steel tee delivers superior strength and resistance to mechanical stress.
Reducer fittings play a vital role in managing diameter transitions within piping systems. The carbon steel reducer is available in both concentric and eccentric configurations to suit various installation requirements. Concentric reducers maintain a symmetrical flow path, ideal for vertical piping arrangements. Eccentric reducers, particularly the reducer pipe variant, prevent fluid accumulation in horizontal lines by incorporating a flat surface on one side.
Specialty fittings address unique system requirements beyond standard connections. Cross fittings enable four-way flow distribution, while caps and plugs provide secure line termination points. Unions offer convenient disconnection points for maintenance purposes, and flanges facilitate connections between different system components or equipment. Each fitting type undergoes rigorous manufacturing processes to ensure compliance with industry standards and performance expectations.
Pipeline Fitting Applications
The application spectrum for pipeline fittings spans multiple industrial sectors with distinct operational demands. In petrochemical facilities, the carbon steel elbow demonstrates exceptional performance in high-temperature hydrocarbon transfer lines due to its thermal stability and corrosion resistance. Commercial plumbing installations frequently specify black steel pipe elbow components for durable, cost-effective water distribution networks.
Process piping systems rely heavily on specialized fittings like the carbon steel reducing tee for controlled fluid distribution in chemical processing units. Power generation applications often require forged steel tee fittings in boiler feed systems where extreme pressures and temperatures demand maximum material integrity. The reducer pipe finds extensive use in water treatment plants for gradual flow velocity adjustments between different pipe diameters.
HVAC installations incorporate these fittings for refrigerant line routing, with the carbon steel 90-degree elbow providing space-efficient directional changes in mechanical rooms. Industrial gas systems utilize black steel elbow components for reliable connections in compressed air and inert gas distribution networks.
Pipeline Fitting Selection
Proper fitting selection requires a systematic evaluation of multiple technical parameters. Material compatibility represents the primary consideration, with the carbon steel 90-degree elbow being specified for corrosive fluid services due to its protective oxide layer formation. The black steel elbow serves as an economical alternative for non-corrosive applications where cost efficiency is prioritized.
Pressure rating requirements dictate wall thickness specifications, particularly for forged steel tee components in high-pressure steam systems. Temperature fluctuations influence material choice, with the carbon steel reducer being preferred for thermal expansion accommodation in heating circuits. Flow characteristics determine fitting geometry, where the carbon steel reducing tee minimizes turbulence in branched fluid systems.
Installation constraints affect configuration selection, with the reducer pipe being specified in space-limited areas requiring compact diameter transitions. Maintenance accessibility often determines whether standard carbon steel tee or specialized forged fittings are employed in particular system locations. Industry standards, including ASME B16.9, ASTM A234, and API 5L, provide essential guidance for specification compliance.
Modern industrial operations depend on precisely engineered pipeline fittings to ensure safe and efficient fluid transport. The technical sophistication of components like the carbon steel reducing tee and forged steel tee enables complex piping networks to function reliably under demanding conditions. Material science advancements continue to enhance the performance characteristics of standard fittings, including the black steel pipe elbow and carbon steel reducer.
A comprehensive understanding of application requirements and fitting capabilities allows engineers to design optimized piping systems. Proper specification, installation, and maintenance of these critical components according to industry standards ensures long-term system integrity and operational safety across all industrial sectors.
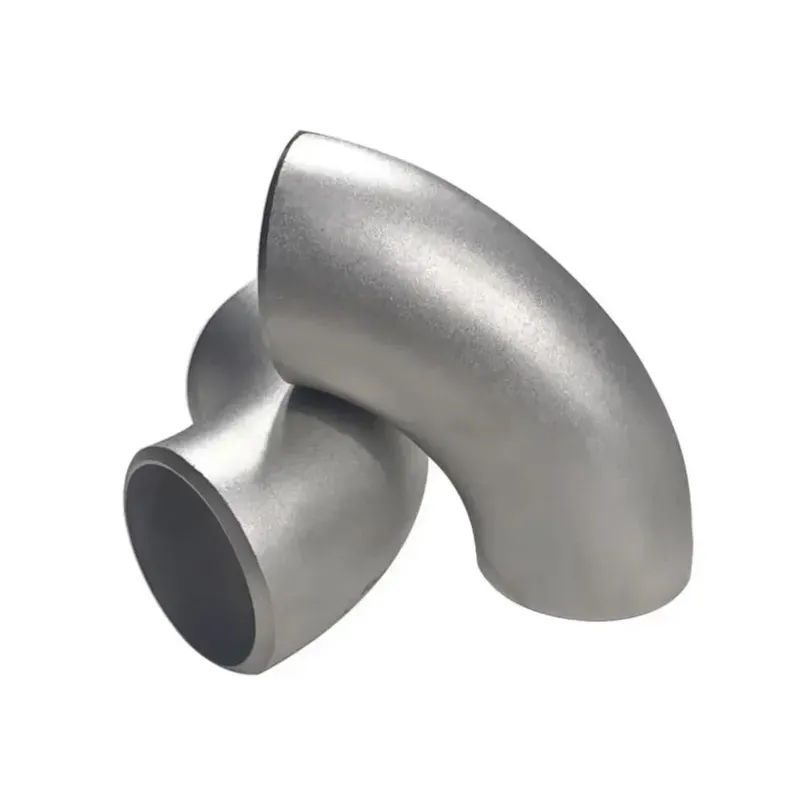