The insulated steel pipe is a critical component in modern industrial and infrastructure projects, designed to enhance thermal efficiency and durability. This article explores the features, benefits, and applications of insulated steel pipe, with a focus on materials such as carbon seamless steel pipes and carbon welded steel pipe, as well as protective measures like anti-corrosion pipe coating. The discussion also covers the role of mechanical steel pipe in various systems, examines key manufacturing standards, and concludes with an overview of its significance in industrial use.
Types of Insulated Steel Pipe
Insulated steel pipe is available in multiple forms, each suited for specific applications. Pre-insulated black steel pipe is commonly used in heating and cooling systems due to its ability to minimize heat loss. This type typically consists of a steel core surrounded by polyurethane foam insulation and an outer protective casing, making it ideal for district heating networks and industrial process piping. The insulation layer significantly reduces energy waste while maintaining consistent fluid temperatures throughout distribution systems.
Carbon seamless steel pipes are preferred for high-pressure applications because of their uniform structure and strength. Manufactured through an extrusion process, these pipes have no welded seams, eliminating potential weak points. This makes them particularly suitable for oil and gas transportation, power generation plants, and chemical processing facilities where system integrity under extreme pressure is paramount. The seamless construction also allows for better insulation application, as the smooth surface provides optimal adhesion for thermal materials.
In contrast, carbon welded steel pipe is cost-effective and widely used in low-to-medium pressure systems. Produced by rolling steel plates and welding the seam, these pipes offer excellent value for water distribution, HVAC systems, and structural applications. Another variant, mechanical steel pipe, is employed in structural and mechanical applications where rigidity is essential, often serving as support columns or machinery components in industrial settings. The choice between these types depends on factors such as temperature requirements, pressure conditions, and environmental exposure.
Anti-Corrosion Protection for Steel Pipes
To extend the lifespan of anti corrosion steel pipe, specialized coatings are applied during manufacturing. Anti corrosion pipe coating serves as a barrier against moisture, chemicals, and other corrosive elements that can degrade pipe integrity over time. Common coating materials include epoxy, polyethylene, and zinc, each selected based on the specific environmental challenges the pipe will face. These coatings are typically applied through spraying, dipping, or wrapping processes, ensuring complete surface coverage.
This protection is particularly important for carbon steel seamless steel pipe and carbon seamless pipe, which are often exposed to harsh environments. Underground pipelines, for instance, require robust coatings to resist soil acidity and moisture, while marine applications demand protection against saltwater corrosion. The coating process involves thorough surface preparation, including abrasive blasting to achieve optimal adhesion, followed by multiple layers of protective material and rigorous quality control inspections.
Properly treated pipes demonstrate significantly improved resistance to rust and degradation, making them suitable for long-term installations in challenging conditions. Advanced coating technologies now incorporate cathodic protection systems for additional defense, particularly in critical infrastructure projects. These combined measures ensure that anti-corrosion steel pipe maintains structural integrity and operational efficiency throughout its service life, even in the most demanding industrial applications.
Manufacturing Standards for Insulated Steel Pipe
The production of insulated steel pipe follows strict industry standards to ensure reliability and safety across various applications. International organizations such as ASTM, API, and ISO have established comprehensive specifications covering all aspects of pipe manufacturing. These standards dictate precise requirements for carbon seamless steel pipes and carbon welded steel pipes, including dimensional tolerances, pressure ratings, and material composition. Compliance with these regulations guarantees consistent quality and performance in end-use scenarios.
Anti-corrosion steel pipe must undergo rigorous testing procedures to verify coating adhesion and resistance to environmental factors. Standardized tests measure resistance to impact, abrasion, chemical exposure, and temperature fluctuations. For mechanical steel pipe, additional structural integrity tests assess load-bearing capacity and deformation resistance. Manufacturers implement quality management systems to monitor every production stage, from raw material selection to final inspection, ensuring all products meet or exceed industry benchmarks.
These manufacturing standards also address insulation materials and application methods for pre-insulated black steel pipe. Specifications cover thermal conductivity values, fire resistance ratings, and vapor barrier properties. Regular audits and certification processes maintain industry-wide consistency, giving engineers and project managers confidence in product selection. As technology advances, standards continue to evolve to incorporate new materials and testing methodologies, further enhancing the reliability of insulated piping systems.
The insulated steel pipe plays a vital role in industrial and commercial systems, offering thermal efficiency, durability, and corrosion resistance. Variants such as pre-insulated black steel pipe, carbon seamless steel pipes, and carbon welded steel pipe cater to different operational needs. Additionally, anti-corrosion pipe coating enhances the longevity of anti-corrosion steel pipe in demanding environments. Strict manufacturing standards further ensure quality and performance. As industries continue to prioritize efficiency and sustainability, the demand for high-quality mechanical steel pipe and insulated solutions will remain strong.
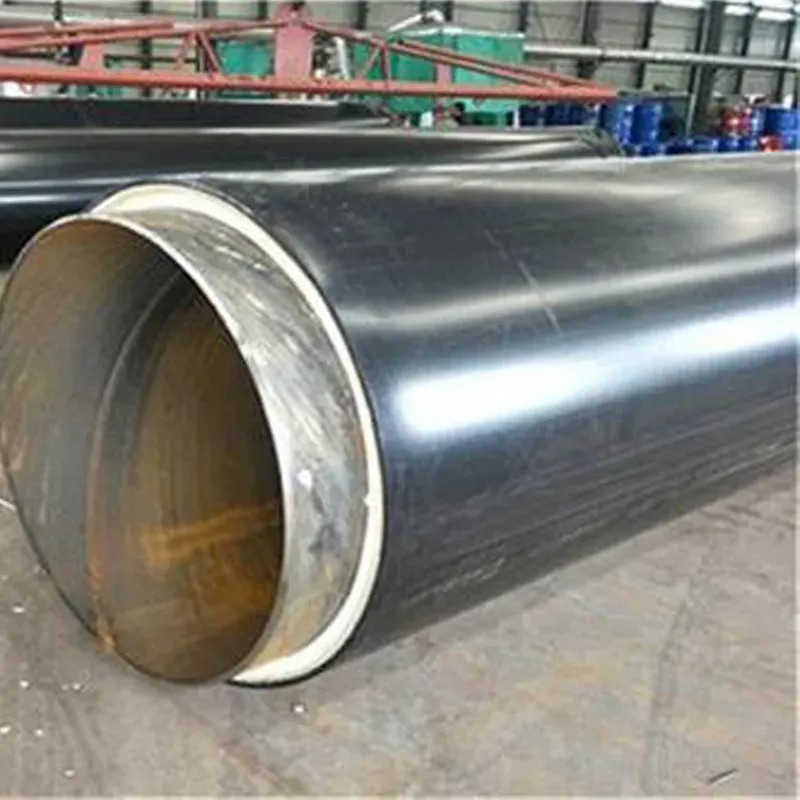