Steel tube types serve as fundamental components across multiple industrial sectors due to their structural integrity, durability, and adaptability. These hollow cylindrical structures are manufactured in various forms to meet specific operational demands. Their classification depends on production techniques, material composition, and intended functionality.
Common Steel Tube Types Based on Manufacturing Methods
The production process significantly influences the mechanical properties and performance of steel tubes. The two primary manufacturing categories are seamless and welded tubes, each offering distinct advantages depending on application requirements.
First of all, carbon seamless steel pipes are manufactured through an extrusion process where a solid steel billet is heated and pierced to form a hollow tube. This method eliminates welded seams, resulting in a uniform structure with superior strength and pressure resistance. Industries requiring high-performance piping, such as oil refineries and power plants, prefer seamless carbon steel tube products due to their reliability in high-stress environments.
Besides, welded steel tubes are fabricated by rolling steel sheets or strips into cylindrical shapes and welding the seams. While this method is more economical and suitable for mass production, welded tubes may exhibit weaker points along the weld line compared to seamless CS pipe alternatives. They are commonly used in structural applications, fencing, and low-pressure fluid transport where extreme durability is not a critical factor.
Furthermore, advanced manufacturing techniques have led to the development of hybrid tubes such as bimetal tube, which combines two different metals to optimize performance. For instance, a steel core with an outer aluminum layer enhances corrosion resistance while maintaining structural rigidity. These tubes are increasingly utilized in chemical processing and marine engineering where environmental factors demand enhanced material properties.
Material-Specific Steel Tube Types and Their Properties
The composition of steel tubes plays a crucial role in determining their suitability for specific applications. Variations in alloying elements and composite materials allow manufacturers to produce tubes with tailored characteristics such as enhanced strength, corrosion resistance, or thermal conductivity. In addition to standard carbon steel options, CS seamless pipe products are widely used in high-temperature and high-pressure systems. Their homogeneous structure ensures consistent performance in demanding environments such as steam boilers, hydraulic systems, and petrochemical plants. The absence of weld seams reduces the risk of failure under cyclic stress, making them a preferred choice for critical infrastructure.
Another notable innovation is the aluminum composite pipe, which integrates aluminum with other metals to achieve a balance between weight reduction and structural integrity. This type of tube is particularly valuable in the aerospace and automotive industries, where lightweight yet durable materials are essential for fuel efficiency and performance.
Similarly, the aluminum plastic composite pipe incorporates layers of plastic and aluminum to provide a versatile solution for plumbing and heating systems. The plastic interior ensures smooth fluid flow and chemical resistance, while the aluminum layer adds strength and prevents deformation under pressure. These pipes are commonly installed in residential and commercial water supply networks.
Finally, specialized components such as the carbon steel reducer are integral to piping systems where diameter adjustments are necessary. These fittings facilitate smooth transitions between pipe sections, ensuring optimal flow dynamics and minimizing turbulence in industrial pipelines.
Key Applications of Different Steel Tube Types
The selection of steel tube types is dictated by operational demands, environmental conditions, and regulatory standards. Each variant offers unique benefits that make it suitable for specific industrial applications.
Seamless CS pipe is extensively employed in the oil and gas sector for transporting hydrocarbons under high pressure. Its robust construction minimizes the risk of leaks and ruptures, ensuring safe and efficient operation in pipelines and drilling equipment. Additionally, power generation plants utilize these pipes in steam and heat exchange systems where temperature fluctuations require durable materials.
Moreover, bimetal tube configurations are increasingly adopted in chemical processing and desalination plants. The combination of corrosion-resistant outer layers with high-strength cores extends the service life of piping systems exposed to aggressive media.
Additionally, aluminum composite pipe is favored in modern architecture for its lightweight properties and aesthetic flexibility. It is often used in curtain walls, handrails, and structural frameworks where both functionality and visual appeal are important. The aluminum plastic composite pipe has gained widespread acceptance in residential and commercial plumbing due to its ease of installation, resistance to scaling, and long-term durability. Its flexibility allows for efficient routing in confined spaces, reducing installation time and labor costs.
Last, carbon steel reducer fittings are essential in complex piping networks, enabling seamless integration of different pipe sizes. Their use in water treatment plants, HVAC systems, and industrial manufacturing ensures efficient fluid control and system compatibility.
The diversity of steel tube types available today reflects the evolving demands of modern industries. From high-pressure carbon seamless steel pipes to corrosion-resistant bimetal tube solutions, each variant is engineered to address specific challenges in industrial applications. Understanding the distinctions between seamless and welded tubes, as well as the advantages of composite materials, allows engineers and project managers to make informed decisions. Whether for infrastructure development, energy transportation, or architectural design, selecting the appropriate steel tube types ensures optimal performance, longevity, and cost-efficiency in any operational context.
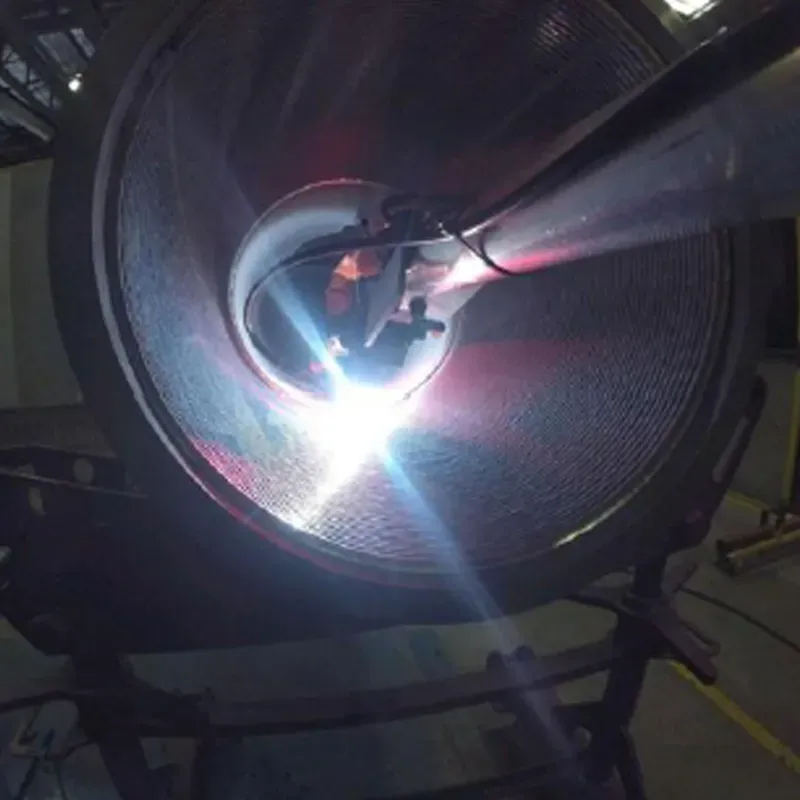