In the vast landscape of industrial production, the sectors related to stålrørsfabrik, composite tube manufacturing, flange manufacturers, flange suppliers, and flange factory form a crucial part of the infrastructure. These industries supply essential components for a wide range of applications, from construction and energy to transportation and manufacturing.
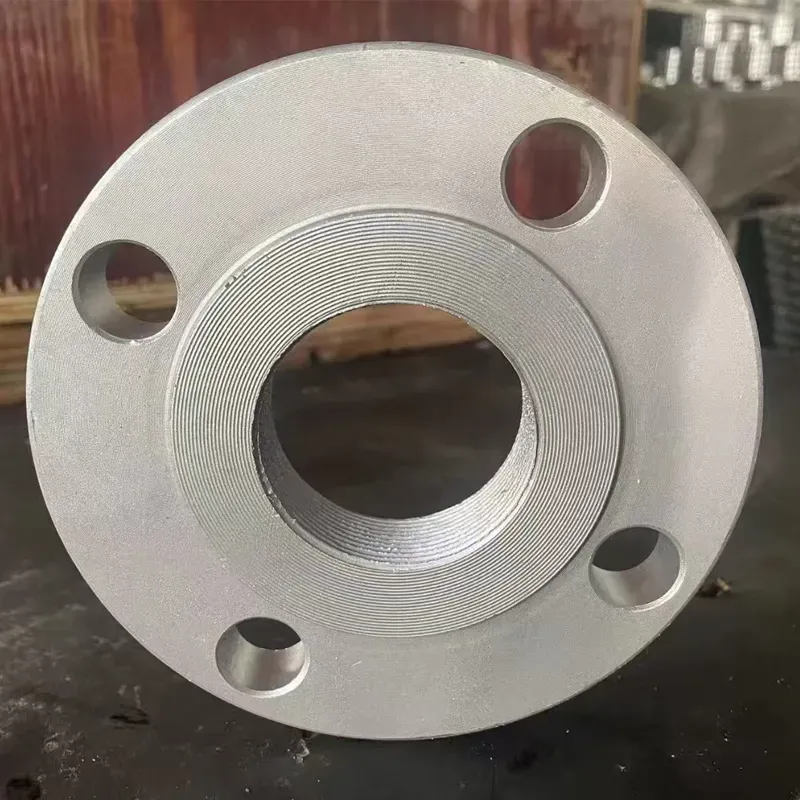
The Role and Operations of Steel Pipes Factories
Steel pipes are integral to numerous industrial and construction projects, and stålrørsfabrik operations are highly specialized. These factories typically start with raw steel materials, which are processed through various methods such as hot - rolling or cold - drawing. In a hot - rolling process within a steel pipes factory, the steel billets are heated to high temperatures and passed through rolling mills to form the desired pipe shape and size. This process is suitable for producing large - diameter pipes used in oil and gas pipelines, where high strength and durability are required.
Cold - drawing, on the other hand, is often used in steel pipes factories for manufacturing pipes with precise dimensions and smooth surfaces. The process involves pulling the steel through a die, gradually reducing its diameter and increasing its length. Steel pipes factories also focus on quality control, subjecting the produced pipes to tests for strength, thickness uniformity, and corrosion resistance. With the increasing demand for sustainable construction, many steel pipes factories are now adopting environmentally friendly production techniques, such as using recycled steel materials and energy - efficient equipment.
Innovation and Applications in Composite Tube Manufacturing
Composite tube manufacturing represents a growing area of innovation in the pipe industry. Composite tubes are made from a combination of materials, typically a matrix material like resin and reinforcing fibers such as glass or carbon fiber. This combination results in tubes that offer unique properties, including high strength - to - weight ratio, excellent corrosion resistance, and good thermal insulation.
In the aerospace industry, composite tube manufacturing plays a vital role. Aircraft components made from composite tubes are lighter, which reduces fuel consumption and increases the aircraft's range. These tubes can withstand high - stress environments, making them suitable for structural applications. In the marine sector, composite tubes are used in shipbuilding due to their resistance to seawater corrosion. Composite tube manufacturing processes often involve advanced techniques like filament winding, where continuous fibers are impregnated with resin and wound around a mandrel to form the tube. This method allows for precise control over the tube's thickness and fiber orientation, optimizing its performance for specific applications.
The Flange Manufacturing Landscape
Flanges are essential components for connecting pipes, valves, and other equipment, and the operations of flange manufacturers and flange factory facilities are key to ensuring a reliable connection. Flange manufacturers use a variety of manufacturing methods, including forging, casting, and machining. Forging is a common method in many flange factories, where heated metal is shaped using compressive forces. Forged flanges are known for their high strength and durability, making them suitable for high - pressure and high - temperature applications in industries like petrochemicals.
Casting, on the other hand, involves pouring molten metal into a mold to create the flange shape. This method is often used for producing complex - shaped flanges in a more cost - effective way. Flange manufacturers also focus on precision machining to ensure that the flanges have accurate dimensions and flat surfaces for proper sealing. Quality control in flange factories is rigorous, with tests for material composition, mechanical properties, and dimensional accuracy.
The Significance of Flange Suppliers
Flange suppliers act as crucial links in the supply chain, connecting flange manufacturers with end - users across different industries. These suppliers maintain a wide inventory of flanges in various sizes, materials, and pressure ratings to meet the diverse needs of their customers. They work closely with flange manufacturers to source high - quality products and ensure timely delivery.
Flange suppliers also provide valuable technical support, helping customers select the right type of flange for their specific applications. For example, in a large - scale construction project, a flange supplier can assist in choosing the appropriate flanges for pipe connections based on factors such as the fluid being transported, the operating pressure, and the environmental conditions. In addition, flange suppliers often offer value - added services like custom - coating of flanges to enhance their corrosion resistance or provide on - site installation support, further streamlining the procurement and implementation process for their clients.
FAQs about Pipe and Flange Manufacturing
How to Select a Reliable Steel Pipes Factory?
When choosing a stålrørsfabrik, several factors should be considered. First, evaluate the factory's production capabilities, including the types of pipes they can produce, their production capacity, and the manufacturing methods they use. Look for a factory with advanced equipment and quality control systems. Check for relevant certifications, such as ISO 9001 for quality management, which indicates that the factory adheres to international quality standards. Customer reviews and references can also provide insights into the factory's reputation for product quality and delivery timeliness.
What Are the Advantages of Composite Tube Manufacturing over Traditional Pipes?
Composite tube manufacturing offers several advantages. Composite tubes are lighter than traditional metal pipes, which reduces transportation and installation costs. Their high strength - to - weight ratio means they can withstand significant loads without adding excessive weight to structures. They also have excellent corrosion resistance, making them ideal for use in harsh environments where metal pipes would corrode quickly. Additionally, composite tubes can be customized to have specific properties, such as enhanced thermal insulation or electrical insulation, depending on the application requirements.
How Do Flange Manufacturers Ensure the Quality of Their Products?
Flange manufacturers implement strict quality control measures. They start by carefully selecting raw materials and ensuring that they meet the required specifications. During the manufacturing process, various inspections are carried out, including visual inspections, dimensional measurements, and non - destructive testing. For forged flanges, the forging process is closely monitored to ensure proper grain flow and strength. After production, flanges are subjected to mechanical tests, such as tensile and impact tests, to verify their strength and durability. Flange factories also maintain detailed records of the manufacturing process and test results for traceability and quality assurance.
What Services Do Flange Suppliers Typically Offer?
Flange suppliers offer a range of services. In addition to providing a wide selection of flanges in stock, they offer technical support to help customers choose the right flanges for their applications. This includes assistance with understanding flange standards, material selection, and compatibility with other equipment. Some flange suppliers also offer custom - fabrication services, where they can modify flanges according to specific customer requirements. Value - added services such as packaging, shipping, and on - site installation support are also common, ensuring a seamless experience for customers from procurement to implementation.
Are There Environmental Considerations in Pipe and Flange Manufacturing?
Yes, both pipe and flange manufacturing have environmental implications. Steel pipes factories and flange factories are increasingly adopting sustainable practices. This includes using recycled materials to reduce the demand for virgin raw materials, implementing energy - efficient production processes to lower energy consumption, and properly managing waste and emissions. In composite tube manufacturing, efforts are being made to develop more environmentally friendly resins and recycling methods for composite materials. By addressing these environmental considerations, the industries can minimize their ecological footprint while meeting the growing demand for their products.