Steel pipes are fundamental components in various industries, including construction, oil and gas, and manufacturing. Customized steel pipe solutions are increasingly in demand due to their ability to meet specific project requirements. This guide explores the key aspects of customized steel pipe, including material options, manufacturing processes, and applications.
Types and Materials Used in Customized Steel Pipe Production
Different projects require different types of steel pipes, depending on factors such as pressure resistance, durability, and environmental conditions. One commonly used material is ST52 3 pipe, known for its high tensile strength and suitability for structural applications. This type of pipe is particularly favored in construction and heavy machinery due to its ability to withstand substantial loads without deformation. Its composition ensures long-term reliability, making it a preferred choice for bridges, building frameworks, and industrial equipment.
Another option is the STPG370 pipe, which is often used in high-temperature and high-pressure environments due to its enhanced mechanical properties. This material is commonly found in boiler systems, heat exchangers, and petrochemical plants where thermal stability is crucial. The pipe's resistance to stress and oxidation ensures prolonged service life even under extreme operating conditions. Its adaptability to various welding techniques also makes it a versatile solution for complex piping networks.
For applications requiring corrosion resistance and flexibility, seamless mild steel pipe is a preferred choice. Its lack of welded seams reduces weak points, making it ideal for hydraulic systems and machinery. Additionally, industries such as automotive and shipbuilding utilize this type of pipe due to its smooth interior surface, which facilitates efficient fluid flow. In cases where lightweight yet durable piping is needed, composite pipe 22mm and custom composite tubes provide an optimal balance between strength and weight efficiency. These materials are often used in aerospace, chemical processing, and specialized industrial systems where traditional steel pipes may be too heavy or prone to corrosion.
Manufacturing and Fabrication of Customized Steel Pipe
The production of customized steel pipes involves precise engineering to meet exact specifications. First of all, raw materials are selected based on the intended application, whether it involves high-pressure fluid transport or structural support. The selection process includes rigorous testing for chemical composition, mechanical strength, and resistance to environmental factors. This ensures that the final product will perform reliably under the expected operating conditions.
Besides material selection, the manufacturing process may include welding, cold drawing, or extrusion, depending on whether seamless or welded pipes are required. Seamless pipes are produced through extrusion or rotary piercing, resulting in a uniform structure with no weak joints. Welded pipes, on the other hand, are formed by rolling steel plates and welding the edges, making them more cost-effective for certain applications. Advanced techniques such as laser cutting and CNC machining further enhance precision, allowing for exact customization in terms of diameter, thickness, and length.
Prefabricated pipework is another critical aspect, where pipes are pre-assembled into modules before installation. This approach reduces on-site labor and ensures higher accuracy in complex piping systems. Factories specializing in customized steel pipe often employ automated welding and fitting processes to create pre-engineered pipe spools that can be quickly installed at the project site. Last, rigorous quality control measures, including hydrostatic testing and ultrasonic inspections, ensure that each customized steel pipe meets industry standards before deployment. These tests verify structural integrity, leak resistance, and overall durability, guaranteeing optimal performance in real-world applications.
Applications and Benefits of Customized Steel Pipe
The versatility of customized steel pipe makes it indispensable across multiple sectors. In the oil and gas industry, STPG370 pipe is frequently used in pipelines due to its ability to withstand extreme conditions. These pipes are designed to handle high-pressure crude oil and natural gas transportation, ensuring minimal risk of failure even in harsh environments. Their durability reduces maintenance costs and extends the lifespan of pipeline infrastructure.
The construction sector relies on ST52 3 pipe for frameworks and support structures, benefiting from its high load-bearing capacity. Skyscrapers, industrial plants, and large-scale infrastructure projects often incorporate these pipes due to their structural reliability. Additionally, their adaptability to different welding and joining techniques allows for flexible design configurations, accommodating various architectural and engineering requirements.
Furthermore, seamless mild steel pipe is widely employed in automotive and machinery manufacturing, where precision and durability are essential. These pipes are used in hydraulic systems, fuel lines, and exhaust components due to their resistance to internal and external stresses. For specialized applications such as aerospace or chemical processing, composite pipe 22mm and custom composite tubes offer superior resistance to corrosion and chemical degradation. The use of prefabricated pipework further enhances efficiency in large-scale projects by minimizing installation time and reducing potential errors.
In conclusion, customized steel pipe solutions provide tailored performance for diverse industrial needs. By selecting the appropriate materials and employing advanced fabrication techniques, manufacturers can deliver piping systems that optimize efficiency, durability, and cost-effectiveness. Whether for high-pressure pipelines or lightweight structural components, customized steel pipe remains a critical element in modern engineering and infrastructure development.
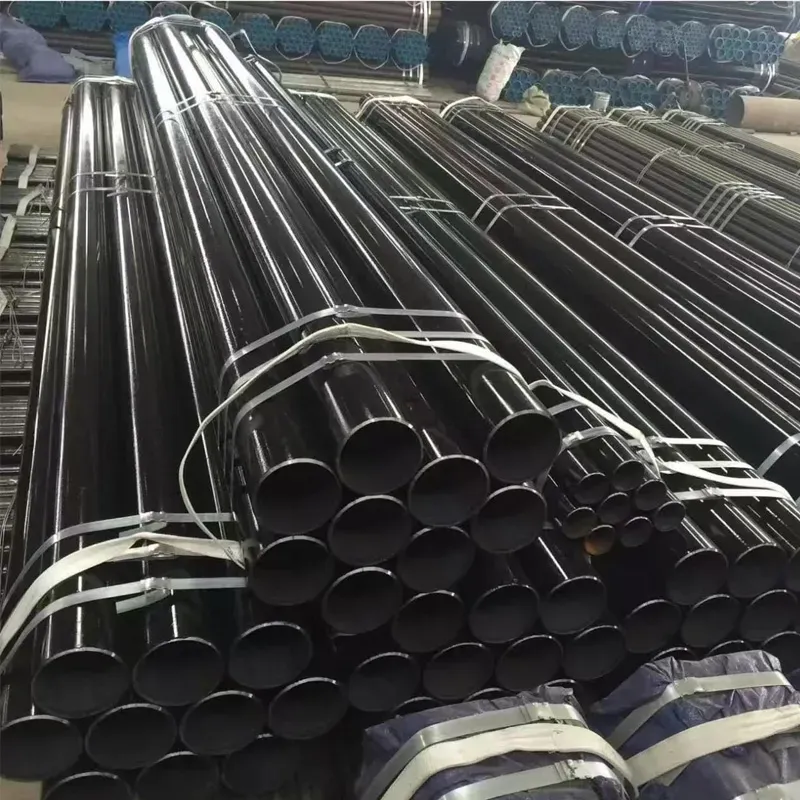