Anti-corrosion pipes are essential components in industries where durability and longevity are critical. These pipes are designed to resist chemical degradation, environmental wear, and mechanical stress, ensuring reliable performance in demanding applications. This article explores the anti-corrosion pipe manufacturing process, its industrial uses, key components such as prefabricated pipe systems and specialized flanges, as well as maintenance and inspection best practices.
Anti-Corrosion Pipe Manufacturing Techniques
The production of anti-corrosion steel pipe begins with stringent material selection. High-grade steel alloys are chosen based on their chemical composition and mechanical properties to ensure optimal corrosion resistance. Manufacturers typically use carbon steel or stainless steel as base materials, with additional alloying elements like chromium or nickel for enhanced performance in specific environments.
Surface preparation is the most critical stage in anti-corrosion pipe coating application. The steel surface undergoes abrasive blasting to achieve a clean, rough profile that promotes coating adhesion. This process removes mill scale, rust, and contaminants while creating an anchor pattern for the coating to grip. International standards such as SSPC-SP10/NACE No. 2 specify the required surface cleanliness and profile depth for different service conditions.
The final manufacturing phase involves applying protective coatings through various methods. Fusion-bonded epoxy (FBE) coatings are commonly applied through electrostatic spraying, while polyethylene coatings are extruded onto the pipe surface. For prefab pipe sections, the coating process may occur before fabrication to ensure complete coverage. Quality control measures include holiday detection tests and adhesion checks to verify coating integrity before pipes enter service.
Industrial Applications of Anti-Corrosion Pipe
In the oil and gas industry, anti-corrosion pipe plays a vital role in both upstream and downstream operations. Offshore platforms utilize specially coated pipes that withstand seawater immersion and high-pressure conditions. These pipes often feature additional cathodic protection systems to prevent galvanic corrosion. The internal surfaces may also receive special linings to resist sour gas corrosion caused by hydrogen sulfide exposure.
Water infrastructure projects extensively use anti-corrosion steel pipe for municipal supply and wastewater systems. Ductile iron pipes with cement mortar linings provide cost-effective corrosion protection for potable water distribution. In wastewater treatment plants, pipes with high-density polyethylene (HDPE) linings resist chemical attack from sewage and treatment chemicals. These systems often incorporate camlock flange connections for easy maintenance access at critical points.
The chemical processing industry requires specialized prefabricated pipe solutions for handling aggressive media. Pipes may be lined with PTFE, rubber, or glass-reinforced epoxy, depending on the chemicals being transported. Flange connections like faucet flange and female flange designs allow for secure joining while maintaining chemical resistance. These systems often operate under strict regulatory requirements to prevent leaks and environmental contamination.
Maintenance and Inspection of Anti-Corrosion Pipe
A comprehensive inspection program is crucial for maintaining anti-corrosion pipe integrity. Operators should establish regular inspection intervals based on pipe location, service conditions, and historical performance data. Above-ground piping requires visual examination for coating damage, while buried pipes may need specialized techniques like close-interval potential surveys to detect coating breaches.
Non-destructive testing methods provide valuable insights into pipe condition without requiring system shutdowns. Ultrasonic thickness gauging monitors wall thickness reduction from internal corrosion. Radiographic testing can reveal hidden defects in welds and fittings. For prefab pipe systems with camlock flange connections, inspectors should pay special attention to gasket condition and bolt tightness during routine checks.
Effective maintenance strategies combine proactive repairs with predictive monitoring. When anti-corrosion pipe coating damage is detected, prompt repairs using compatible materials prevent further deterioration. Cathodic protection systems require regular potential measurements and rectifier checks. Maintenance records should document all inspections and repairs to support asset management decisions and regulatory compliance.
The widespread adoption of anti-corrosion pipe across industries demonstrates its critical role in modern infrastructure. From manufacturing processes that ensure long-term durability to specialized applications in harsh environments, these piping solutions address the fundamental challenge of material degradation. The development of advanced anti-corrosion pipe coating technologies continues to expand the service life and reliability of piping systems in increasingly demanding conditions.
Looking forward, the integration of prefab pipe systems with smart monitoring technologies represents the next evolution in corrosion management. Innovations in flange designs, including improved female flange and camlock flange configurations, will further enhance installation efficiency and maintenance accessibility. As industries face stricter environmental regulations and economic pressures, anti-corrosion steel pipe will remain an essential component for safe and sustainable operations across multiple sectors.
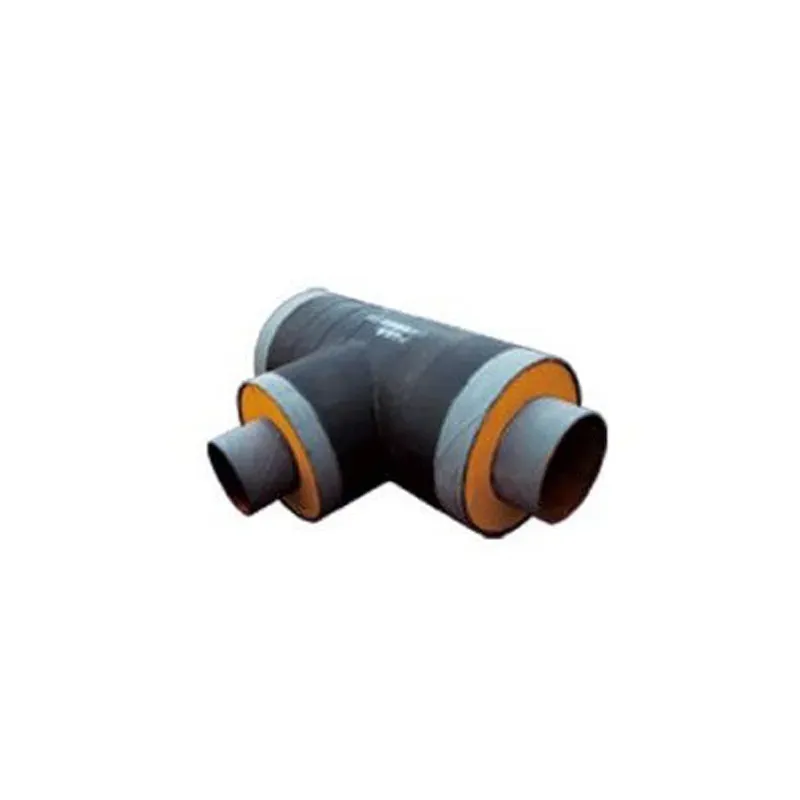