Prefabricated pipework offers a streamlined solution for industrial piping systems, ensuring efficiency, durability, and cost-effectiveness. This article explores the benefits, materials, applications, and industry standards of prefab pipe systems, focusing on A179 steel, SA179 tubes, and aluminium composite pipe options. Examining these components highlights how prefabricated pipework meets diverse industrial demands while maintaining high performance and reliability.
The Advantages of Prefabricated Pipework
The primary benefit of prefabricated pipework lies in its ability to significantly reduce project timelines. Unlike traditional piping methods that require extensive on-site fabrication, prefab pipe systems arrive at installation sites as complete assemblies. This approach eliminates the need for time-consuming field measurements, cutting, and welding operations. Projects utilizing prefabricated pipework typically experience 30-50% faster completion rates compared to conventional methods.
Beyond time savings, prefabricated pipework offers superior quality control. Factory production environments allow for precise manufacturing under controlled conditions, ensuring consistent weld quality and dimensional accuracy. Each prefab pipe component undergoes rigorous testing before shipment, minimizing the risk of defects that might occur with on-site fabrication. This level of quality assurance is particularly crucial for critical applications in the oil and gas or chemical processing industries.
The modular nature of prefabricated pipework also provides exceptional flexibility for system modifications and expansions. As industrial facilities evolve, prefab pipe systems can be easily adapted or extended with minimal disruption to operations. This modularity proves especially valuable in maintenance scenarios, where specific sections can be replaced without requiring complete system shutdowns. The standardized connections in prefabricated pipework ensure compatibility across different project phases and system upgrades.
Materials Used in Prefabricated Pipework
A179 steel and SA179 tubes represent the gold standard for heat transfer applications in prefabricated pipework. These low-carbon steel materials exhibit exceptional thermal conductivity, making them ideal for heat exchangers, condensers, and other temperature-sensitive systems. The seamless construction of SA179 tubes ensures reliable performance under high-pressure conditions, while their corrosion-resistant properties extend service life in demanding environments. These materials maintain structural integrity even when exposed to continuous thermal cycling, a common challenge in power generation facilities.
For applications requiring lightweight solutions, aluminum composite pipe offers an excellent alternative to traditional steel systems. The aluminium composite pipe variant combines the strength of metal alloys with the corrosion resistance of specialized coatings, making it particularly suitable for marine and offshore installations. This material demonstrates remarkable resistance to saltwater corrosion while maintaining sufficient structural strength for most industrial applications. The reduced weight of aluminum composite pipe systems also translates to lower transportation and installation costs compared to their steel counterparts.
Material selection for prefabricated pipework must also consider chemical compatibility and operational temperatures. While A179 steel performs exceptionally well in high-temperature steam applications, certain chemical processes may require specialized alloys or lined piping systems. Modern prefab pipe solutions can incorporate various lining materials, from PTFE to ceramic composites, to handle aggressive media. This customization capability ensures prefabricated pipework can meet the specific demands of pharmaceutical, food processing, and semiconductor manufacturing industries.
Industry Standards for Prefabricated Pipework
The manufacturing of prefabricated pipework adheres to stringent international standards to ensure system reliability and safety. ASTM specifications govern the production of A179 steel and SA179 tubes, dictating precise chemical compositions, mechanical properties, and testing protocols. These standards guarantee that materials used in prefab pipe systems will perform as expected under design conditions. Compliance with these specifications is verified through material test reports and certification documents accompanying each shipment.
Quality control processes for prefabricated pipework extend beyond material specifications to include comprehensive fabrication standards. Welding procedures must qualify under ASME Section IX requirements, with welders holding appropriate certifications for the specific materials and joint configurations. Non-destructive examination methods, including radiographic testing and ultrasonic inspection, verify the integrity of all critical welds in prefab pipe assemblies. These rigorous inspection protocols help detect potential flaws that could compromise system performance.
The installation and maintenance of prefabricated pipework also follow established industry best practices. Design organizations like ASME B31.3 provide guidelines for pressure piping installation, while API standards offer specific recommendations for oil and gas applications. These standards ensure proper system integration and long-term reliability. Furthermore, many prefabricated pipework manufacturers provide detailed installation manuals and technical support to facilitate the proper implementation of their systems in various industrial settings.
Prefabricated pipework delivers efficiency, reliability, and adaptability across multiple industries. By leveraging materials like A179 steel, SA179 tubes, and aluminum composite pipe, these systems meet rigorous operational demands while optimizing installation and maintenance. Adherence to industry standards further enhances their reliability, making prefab pipe solutions a practical choice for modern infrastructure. As industrial needs evolve, prefabricated pipework will continue to play a vital role in efficient system deployment.
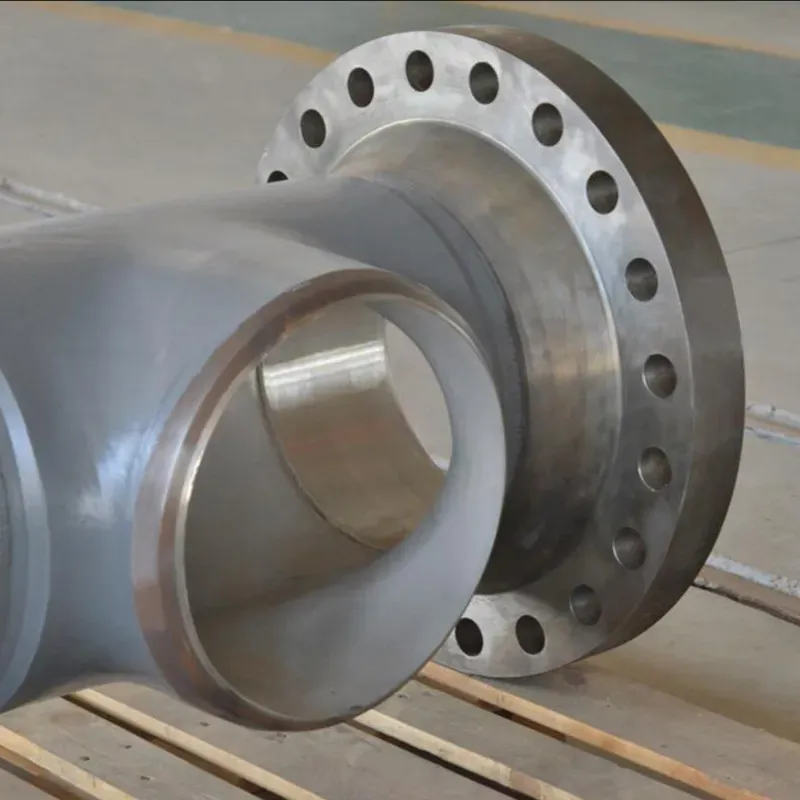